With Guest Daniel Oberhänsli, CEO of suicorr AG (a Cathodic Protection Company)
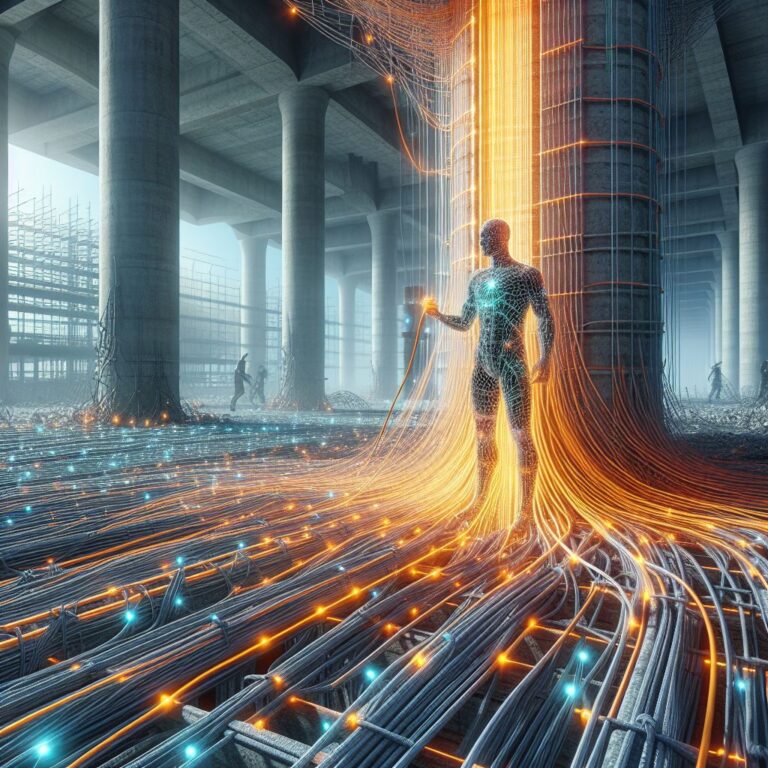
Summary
Learn all about Cathodic Protection in Reinforced Concrete, a pioneering innovation in modern construction engineering. Cathodic Corrosion Protection (CCP) safeguards reinforced concrete from corrosion through a electrochemical process and extends the lifespan of structures. Discover how CCP is utilized in various projects and explore the benefits of CCP, including environmental friendliness and cost-effectiveness. Let CCP inspire you and build safer and more durable infrastructure.
Applications of Cathodic Protection in Concrete
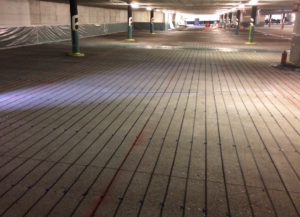
Car Park Sihlcity, Zürich
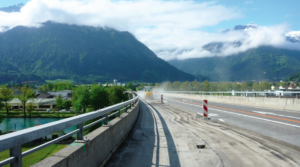
Swimming Pool Schoolhouse Kleinhüningen
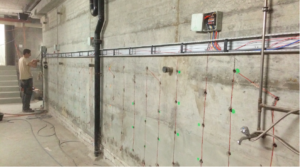
Bridge Goldswilviadukt, Interlaken
Translated Podcast Transcript
Johannes: Our topic today is Cathodic Protection in Concrete. We’re talking to Daniel Oberhänsli. He’s been the CEO of Suicorr AG for 12 years, offering CCP (Cathodic Corrosion Protection or Cathodic Protection) systems to its customers. We’ll explain what CCP is in a minute. Daniel is a construction engineer, and he impressed me with his clear way of speaking and his experience in a course we both presented. I hope he will do the same in podcast format. Welcome to Concretely, Daniel.
Dr. Oberhänsli: Johannes, thank you for the invitation. I am very happy, and I’m curious to see whether I can do this in this format and explain cathodic corrosion protection to everyone.
Johannes: Daniel, the Romans built the roof of the Pantheon in Rome 1900 years ago, which still stands today, using a previous version of today’s concrete. To start with a “simple” question: what do you think would have happened if the Romans had invented the steel-reinforced concrete we use today and built the Pantheon roof with it?
Dr. Oberhänsli: Exciting question. I think we have to delve deeper and briefly think about why we have steel in concrete. The Pantheon has no steel, and what is the reason for that? Steel is responsible for transferring tensile forces, and the rest is taken over by the mortar or the concrete itself.
If the Romans had taken this idea of transferring forces to steel, I assume the Pantheon would look completely different. They would have had completely different possibilities. The steel would have been useful only in this way. So, the question is, if we had built a structure 1900 years ago based on steel-reinforced concrete,
What would have happened? It is safe to assume that this structure would have had to deal with corrosion problems, as we see with many younger buildings today. Yes, so I think corrosion would have been an issue. And whether the structure would still be standing today is questionable.
Johannes: I think so too. At the end of the 19th century, reinforced concrete was discovered, developed, and commercialized in the DACH area, then brought to the USA. We will make a separate episode about the exact story.
But the fact is that at the time, it was thought that the application of iron in concrete was very well protected, or passivated, due to the high alkalinity of the concrete. It was thought that it could not rust there. But today, it looks completely different.
In a study in the 90s, conducted in the USA, it was found that the corrosion of highway bridges in America alone cost the taxpayer 8 billion dollars a year. A study initiated by NACE International; I will give the link in the podcast description. And in 2020, there was also a study in Switzerland, where it was found that bridge corrosion costs the taxpayer 1000 francs per minute. What exactly happens with corrosion that we would wish today’s bridges to last 80 years, compared to the Pantheon?
Dr. Oberhänsli: You said it correctly earlier. A few decades ago, it was assumed that steel in the concrete is constantly protected. Before we talk about corrosion, we have to take a step back and consider corrosion protection. As mentioned, concrete generates an extremely high-alkaline environment, especially due to cement.
This means we have, in healthy, fresh concrete, usually pH values around 11 or 12, something like that. And if we now insert steel, let’s say normal C steel, into this environment, a passive film naturally forms on the steel surface. This is an ultimately thin, only a few nano-layers thick film, which provides corrosion protection to the steel
A side note, this is not the case with every metal. With aluminum, for example, it would be the opposite. If we put aluminum in this high-alkaline environment, the aluminum surface would start to corrode because it is unstable in this environment. Aluminum is stable in the neutral environment, pH value 7, as we normally find it. Steel is not stable there.
So, if this passive film, this high alkalinity, was permanently present, we would actually have an absolutely ideal combination between steel and concrete. Now different things can happen, so that this corrosion can run off despite this “ideal” connection.
There is one phenomenon, which is the so-called “carbonatization”. That means the surrounding steel loses its high pH value by environmental influences. This process is called carbonatization. This process begins on the environmentally exposed side and slowly feeds into the concrete.
It is important to know that this process is not linear, but the speed of this neutralizing processes decreases, and it will eventually fall asleep. Today we recognize the tendency that we have to implement higher iron coverage compared to high-conjunction structures. And with that, our constructions are certainly much better protected from this influence than a few years ago.
That’s one thing. The other corrosion-reducing problem is the winter service, or simply chloride-ingress in our construction. In Central Europe, it is certainly less due to sea water, but as mentioned, the winter service. In the winter service, de-icing salt is brought out onto the streets, i.e., sodium chloride (NaCl). And this chloride-ingress of the de-icing salt can locally destroy the passive film, which leads to corrosion or an unprotected area in this part.
So, if the reinforcement steel in the concrete is no longer surrounded by this passive film, the steel in these specific areas is less noble than on the area where the passive film is still intact.
And now we have the phenomenon that we can actually compare very well with a battery or a galvanic element (which is the technical term). At the point where the passive film is destroyed or affected, we have the minus pole. And we have the plus pole next to it, where everything is okay. We have a metallic connection between these two poles.
The remaining moisture in the concrete is sufficient to have an electrolyte. This is how a small corrosion cell begins to become active, a small galvanic element, where the steel dissolution begins to start in the anode, i.e., in the destroyed area of the passive layer.
And now there is actually permanent flow, a very, very little current, but since this is really permanent, it can lead to several millimeters per year of reinforcement steel cross-section loss in extreme cases, especially with chloride-induced corrosion. This is the main mechanism.
What I would like to point out at this point is that with a corrosion cell that has been created by carbonatization, the rate of corrosion, i.e., the speed, is usually smaller and is usually visually recognizable on the concrete surface. With chloride-induced corrosion, the corrosion rate or metal absorption is generally more profound. Moreover, and this is very dangerous and sneaky, it does not necessarily have to be, that this corrosion process is visual on the surface in form from concrete spalling, corrosion products or cracks. So, reinforcement steel can be fully corroded (separated), although I don’t know much about it on the surface.
Johannes: As expected, that was explained extremely well. Thank you, Daniel. I like the fact that you point out that chloride-induced corrosion often can’t be seen, which is a problem because nowadays a lot of structures are visually inspected.
The fact that the carbonatization induced corrosion is slower, also has to do with the fact, that it is more large-scale and that the negative pole (Anode) on the rebar is larger compared to chloride induced corrosion, where the Anode is very small (pitting corrosion) and therefore the corrosion rate faster.
Dr. Oberhänsli: This is one of the main parameters in a corrosion cell. There are of course many other parameters that positively or negatively influence the corrosion, be it moisture, be it the conductivity of the concrete, be it the exposure, steel type etc. But these surface conditions are certainly a decisive point in the case of hole-face corrosion.
Johannes: And above all, you said that the residual moisture is sufficient for the concrete to act as an electrolyte. It was not clear for me in the beginning, that concrete is still moist inside from the time it was mixed with water and applied. That is what you mean by residual moisture, right?
Dr. Oberhänsli: This certainly on the one hand, but we must also see that I have a completely different room climate in a basement garage than if I had the same phenomenon in a high-rise building. So, it can also be that if I now have a chloride-induced corrosion, in an environment like a basement garage, a bridge or another exposed object. But I could use manual, controlled evaporation to bring this corrosion process to a halt.
So basically, by increasing the resistance (through less moisture and therefore higher electrical resistance) I can influence the corrosion speed inside the concrete.
But it has to be added that this is not realistic for many objects like, for instance sealing an underground car park in a way that I don’t have any weather influences or moisture.
Johannes: This reminds me of a hydrophobic treatment, which can be helpful to reduce the moisture content of concrete by allowing the (residual) moisture inside the concrete to evaporate (or diffuse) out through the membrane, but by not letting any new liquid water (like splashes) into the concrete.
Dr. Oberhänsli: This is certainly a positive aspect. Yes, exactly. But it is also important to consider with caution: How long-term is the solution? How much moisture is left in the concrete? To what depth will this moisture sink through such a measure?
Johannes: Okay. And do you think that 80 years of life, as many assume, is realistic for exposed concrete structures like bridges? Or could a problem occur earlier?
Dr. Oberhänsli: I think that the life expectancy of 80 to 100 years is basically realistic. I therefore find that we have a quality and knowledge problem today… or a problem of implementation, that we actually knew how it would work, but we also have different boundary conditions that prevent us to implement accordingly. So, I do believe that there are still many options available today.
Be it with cathodic corrosion protection, but also with conventional, classic protection mechanisms or methods and possibilities to extend the lifetime.
Your question was kept very generally. There are certainly also differences in the individual structures. There are for instance highly exposed components, where that may require certain interventions during their lifetimes. There I think maintenance and surveillance are of high importance. And there are objects where I can certainly secure a high lifespan with less effort. But I think it’s realistic.
Johannes: The key word “cathodic corrosion protection” (CCP), so we are slowly getting to the main topic. In the 60s and 70s, there was a construction boom in Europe. In Switzerland, for example, at the height of this construction boom, over 200 motorway bridges were built per year. They are now about 60 years old. Many of them are older.
That means our infrastructure is getting old. It’s aging quickly. And there is this solution, the CCP, which is already used a lot in other industries, for example in the oil and gas industry, to protect all the pipelines, but also in shipping, to protect the hull of ships from sea salt. Can you maybe explain, as clearly as before, what cathodic corrosion protection is?
Dr. Oberhänsli: I am happy to accept this challenge and hope that I can cover the needs or expectations accordingly.
Let’s start by understanding the conventional approach. How does it work and what is the purpose? If we have a chloride-contaminated structure or a carbonized structure, then in a large number of cases we have to remove the harmful concrete, replace it with new concrete or mortar, then coat this surface and hope that no more chloride or harmful substances can enter and finally hand over the system to itself.
Now, when it comes to cathodic corrosion protection, we don’t want to directly affect the chloride or these carbonatization phenomena, but we want to counteract the electrochemical process.
And this is exactly the same approach as you mentioned before, whether it is in the oil and gas industry or in the shipping industry, etc., the philosophy is quite similar. So, we want to introduce a new anode in the system, and we want to give a little bit of electricity from this anode to the environment, to influence existing anodes on the steel reinforcement and stop the corrosion processes. So, we want to bind the corrosion current in the construction by an external current, or reduce it to a technically feasible level, as the correct definition goes.
As a result, these reinforcement steel corrosion currents have no influence or negative usage restrictions.
If we think about what that means, let’s assume that we have a park deck that is now saturated with chloride and a measure has to be taken. If we want to apply a cathodic corrosion protection, then it naturally requires various pre-clarifications and a definition: whether you now have to protect the entire cross-section, only the upper deflection layer etc. But basically, in the course of the process, you have to get an anode system on the surface.
In contrast, for example, when we build pipelines, we build a very local anode and then this local anode protects the steel surface for over 10 kilometers. In the reinforced concrete construction, it behaves in such a way that we must cover the entire protective area with an anode system.
The concrete is then prepared and roughened so that a later to be applied re-profiling mortar or concrete can connect to the underground. Once this underground preparation is completed, the anode is installed on the surface. These are titanium grids or titanium bands. Today carbon grids or special conducting coatings are also used.
These anode networks are supplied with power connections. The same way the reinforcement bars are supplied with power connections (actually, these are more like power backflow connections, because the power is then fed back through these connections). These carbon or titanium grids are then embedded in a reprofiling mortar. The layer thickness of this reprofiling mortar is about 10 – 20 mm.
And certain monitoring sensors are installed and then a voltage is applied between this anode system, which was applied, and the reinforcement steel that is in the construction. This voltage is a direct current (DC) voltage. We have an order of magnitude between 1 and 3 volts. So, it’s a very low tension.
You might remember when you sit in front of the TV at home and want the remote control doesn’t react, you can take the battery out of the battery compartment and test it with your tongue to see if it still has voltage. This is the 9-volt battery. You then put 9 volts on your tongue to see if it still tingles on your tongue, if there is still voltage. 9 volts. I just mentioned that for CCP in reinforced concrete we usually apply something between 1 and 3 volts.
That means that for humans and animals this voltage is not dangerous. We are in the absolute smallest range of voltage. And in terms of overall performance, you can take it as a rule of thumb that for about 1000 m2 of reinforced concrete or steel surface that you want to protect, you may need a power of 20 watts.
So, fundamentally speaking, to protect a 1000 m2 of steel surface, a fluorescent tube that is constantly shining in the underground garage. These are small streams, but they have a very big effect.
This is the general structure of how a CCP is designed.
Johannes: Is there always external power or is there a case that the potential difference between the new anode (i.e. titanium grid) and the cathode (protected reinforcements steel) is sufficient?
Dr. Oberhänsli: That’s a good question. There are systems that work with victim’s anodes. That means I bring a less noble material to my steel surface. I consciously contact it directly with the reinforcement steel to be protected. The anode that has been applied now sacrifices itself, dissolves itself, to protect the steel.
The systems are available on the market. I find that the systems are applied less often than the once with external current. Because I can’t regulate such systems. The surveillance is a bit more demanding or more limited. But especially the regulation of such systems and the voltage difference that is then given, which I can’t influence, these are arguments why on the market, there are a very large amount of these foreign power systems.
Side note: in the German speaking market.
Johannes: Your company is offering this CCP system to its customers. Can you give us an overview of the application areas?
Dr. Oberhänsli: Sure. We must differentiate briefly. I’ll start with a general approach. Suicorr AG offers services in German-speaking Europe, especially for reinforced concrete, which we just discussed. We’ve also specialized in the market of settlement water management. This involves issues like brown spots forming on the water-containing surfaces of many drinking water containers. These phenomena can be prevented and frozen with a certain amount of electricity. Suicorr is also in the pipeline market, serving the oil, gas, and water industries, protecting transport lines of various sizes.
In the area of reinforced concrete construction, our application fields are extremely broad. We’ve worked on objects as small as 14 m². The conditions there were so special and restrictive for a conventional installation that the CCP was a quick, simple, and effective solution for this 14 m².
This can be scaled up to the largest object currently in our portfolio, about 20,000 m², a full-scale installation in a large car park where corrosion is a constant issue. Our service portfolio also includes bridges, underpasses, arcades, tunnels, etc.
We haven’t mentioned this before, but 90-95% of our projects are with existing structures, meaning we build on the existing portfolio, where we’ve identified a damaging impact and then developed a package of measures. But cathodic corrosion protection (CCP) is also a preventive measure.
For example, we were allowed to equip certain areas during the pre-works for the second tube of the Gotthard Road tunnel across the Gotthard massif. This ensures that even in the future, when chloride will inevitably enter the construction, we are already prepared to face this challenge.
Johannes: I can understand that for a critical infrastructure like the Gotthard tunnel, an important economic route between Italy and Northern Europe, you’d want to take fewer risks. In parking garages, the corrosion problem arises from chlorides brought in by cars. Generally, is there a tendency to apply CCP to prevent chloride-induced corrosion?
Dr. Oberhänsli: Most of our projects are based on chloride-contaminated challenges. We have very few requests in the field of carbonatization. Then it might be more about monument care, or special objects that are the trigger.
But it has definitely been recognized correctly. We are mostly in the reinforced concrete industry when it comes to chloride-induced corrosion.
Johannes: How new is the cathodic corrosion protection system in reinforced concrete construction? Since when is it used?
Dr. Oberhänsli: I will take another step back. The origin of this system comes from the pipelines. We have known this since around 1900, when it was used for the first lines and saw effects. A little before that, it was even the case that they wanted to protect ship hulls, that’s where it really comes from, against corrosion in the long run. And then it was realized that if you work with different metals, then this resolution seems to be less for my actual to be protected material. And so, it was refined and transferred to pipelines, to steam tanks.
And then, finally, I don’t remember the year, but I think it was around 1960, at the end of the 60s, the first bridge with cathodic corrosion protection was built in the USA.
In Europe, it was in the late 80s. There was an object in Berlin that was then rebuilt as part of a highway expansion. At the same time, there was an installation in Switzerland in 1987-1988. This installation is still functional today and is regularly checked.
This is a column and thrust bearing of a bridge, located on a canton street, of the canton of Tessin. This object is located near the village Rodi-Fiesso and crosses the Gotthard Mountain route of the Swiss Federal Railways, the SBB. This column and thrust bearing were quite intensively contaminated with chloride and it was decided to apply cathodic corrosion protection. So today we have an object that has been running on the network for almost 35 years and is still operating. And to this day, there were no further refurbishments required. And there are still no concrete spallings, no corrosion phenomena to be seen, although the chloride has been in the construction for 35 years but is protected by the cathodic corrosion protection.
Johannes: Interesting. I find it particularly exciting that the system has apparently been around since the 19th century and that it was only started 60 years later in reinforced concrete structures, showing a bit how the corrosion problem has become bigger and bigger at the end of the last century.
A question that I thought about that I find interesting, today new materials are used again, one of which is UHPC, but above all, many more CO2-friendly cements are being developed and applied. What needs to be considered when applying these new materials for the application of cathodic corrosion protection?
Dr. Oberhänsli: There are certainly two aspects that should be mentioned in my opinion. One is that when we use CO2-reduced cement, the composition of this cement is essential. When it comes to cathodic corrosion protection, it is relevant that the current that I apply to these anodes, which I mentioned are applied on the surface. That this current, can flow through the object onto the iron and penetrate it and can develop its protective effect there. So, if I change this path, this electrolyte between anode and cathode, and for example generate an increased electrical resistance in between, then it becomes more challenging for cathodic corrosion protection. I have to drive with higher voltages, then I may have issues with homogeneity, current distribution, life span of the CCP, etc. So
the CCP’s demand would be to have a little, and not an extremely high resistance between the anode and cathode. For example, epoxy binding agents would hinder the functionality of cathodic corrosion protection. That’s one thing: Electric resistance development of these new cement types.
The second thing that you might have to consider. Let’s take a closer look at electrochemistry. On the cathode side, that is, on the steel reinforcement, we produce OH- ions. So, there will be a pH value increase directly on the steel itself. But on the anode side, we will also produce acid.
Depending on the operating level, the height of the voltage and so on, it can actually also lead to acidification directly in the anode area. So, the reprofiling mortar that was put there should have a certain buffer capacity. And now we come to the pH value of the new mortars. Should the new cement types that are introduced, lead to a lower pH value, we have on the one hand the issue that new constructions may no longer have such a high natural corrosion protection for the steel, as was the case with a CEM I, with pure Portland cement. And on the other hand, you have to consider, but we still do not have any results yet, how this will behave with this buffer capacity for acidification.
I think these are developments that you have to keep in mind and observe. But it would be inappropriate for me to say where this journey is going. At the moment I don’t feel competent enough to make a final decision.
Johannes: What are the reasons why construction owners choose against applying a CCP system?
Dr. Oberhänsli: I think a fundamental point is the self-fulfilling prophecy. If it is not used enough, then I am critical of it. But I also have sympathy for this. I am also a civil engineer from the background and not an electric engineer.
And it is also easier for me to imagine that if I have a simple beam and I apply a load, that it bends through and I can imagine that and calculate that, etc. And if I now come to a construction site and say: “Yes, I have a pair of anodes and I put them on the surface and then connect it to two cables and yes, forget the corrosion, now it’s running”. Then there is a lack of imagination for many construction specialists who are at home in the refurbishment world. We are civil engineers, architects, construction managers, etc. and we are not electrical experts. For an electric specialist, it’s much less of a hurdle in understanding the electrochemical process than for a classic concrete refurbishment specialist.
And that already begins with the training, be it in further training, be it in the universities, that cathodic corrosion protection is for many a closed book. But we also note that if a planner, a builder has embarked on this process and has understood that, that he can see a lot of application possibilities and a lot of potential in it, to implement this in the future.
Johannes: That’s very interesting. Another reason I could imagine is that the CCP system might be more expensive than conventional refurbishment techniques at the beginning although it protects longer. Do you think that’s also a reason?
Dr. Oberhänsli: I would strongly contradict the argument that CCP is more expensive than conventional repair. It really depends on the object. As construction specialists, we’re obliged to find the right solution for each site, considering both technical and economic aspects. Cathodic corrosion protection can often be cheaper, especially if there’s a deep chloride intake and large layers of concrete (5 to 8 cm) need to be removed and re-profiled. There are also ecological aspects to consider, and cathodic corrosion protection has great potential in this regard.
CO2 emissions during cement production make it unattractive. If we can reduce these emissions through CCP, because we don’t have to remove as much concrete, and because the system’s lifespan is longer, then that’s another advantage for CCP.
Moreover, from my experience, construction measures with CCP can be significantly faster and involve fewer interventions. For instance, consider a park deck roof where 4 to 6 cm of concrete must be removed. This might require closing the floor below due to the risk of water damage and, potentially, for static reasons. Reducing concrete waste avoids these restrictions. We’re faster because we need less time for concrete hardening. When looking at full construction cost calculations, in many cases, CCP is more affordable.
Often, when considering lifecycle costs, CCP positions us even better, although the system already appears attractive based on construction costs alone.
Johannes: Interesting. I thought that installing a titan grid or cables, and the current, would be more expensive in terms of construction costs. I hadn’t considered the reduced need for concrete removal compared to conventional concrete refurbishment, where you sometimes have to go below the rebar layer. You’re right; there can be many more static considerations that slow down the construction project.
Dr. Oberhänsli: That’s another point. We should ask for which objects CCP no longer makes sense or what prevents CCP from being more widely used. CCP is not a panacea for objects not reaching their design life.
If we encounter an object where static security can no longer be assured because the residual rebar cross-section is too limited, requiring additional rebars or reinforcements, then CCP might not be useful. In such cases, concrete has to be removed to the rebar level to add rebars, making CCP more of a preventive measure for the future rather than a solution. While it’s suitable in many cases, there are conditions that must be met.
Johannes: Are there other challenges in future applications of CCP systems? You’ve mentioned the need to convince construction owners and the fact that the system, although long-established, is still not well known. Are there other challenges?
Dr. Oberhänsli: No, you’ve anticipated them correctly. One challenge is convincing the appropriate experts. The other is that, in my opinion, the potential of cathodic corrosion protection is not yet fully exploited or processed. There’s still a lot to be done in this direction.
Dr. Oberhänsli: I would strongly contradict this argument. Implicitly, you have given the statement that the CCP is more expensive than a conventional repair. I would not confirm that at all. I think it really depends on the object. We as construction specialists are obliged to look for the right solution for the construction site. And that is certainly a technical aspect, but also an economic aspect. And cathodic corrosion protection can also be cheaper in many cases, in regards to the construction costs. If I have a relatively deep chloride intake and I have to remove large layers (5 to 8 cm) of concrete and have to re-profile, then the cathodic corrosion protection quickly becomes cheaper or more valuable than a conventional repair. It’s not just that, there are also ecological aspects in the evaluation of these methods, and I think there is also great potential for cathodic corrosion protection.
Because as you mentioned, the CO2 emissions during production make cement not very attractive. And if I can reduce the CO2 emissions through the use of a cathodic corrosion protection system, because I don’t have to remove so much concrete, because my layer thickness is significantly lower, because my survival time is significantly longer, then that can be another bonus point for CCP.
In addition, from my experience, construction measures with cathodic corrosion protection can be significantly faster and more often with fewer interventions. For example, a park deck roof, where I now have to remove 4, 5, 6 cm of concrete. This means that I have to close also the underlying floor, due to the danger of running water and maybe even at some point due to static conditions. And if I can reduce this concrete waste, I will be able to avoid these restrictions. I am faster because I have to consider less concrete hardening time. And if I look at a full cost construction calculation, in many cases the CCP is clearly more affordable.
Often, latest when looking at the lifecycle costs, it helps us to be positioned even better, although the CCP system already looks very attractive with the construction costs.
Johannes: Okay, interesting. I thought that because you have to install this titanium grid or maybe you have to apply cables and the current it would be more expensive in regards to construction costs. But of course, I did not consider that you have to remove much less concrete, in some cases, compared to a conventional concrete refurbishment, where you sometimes have to go down below the rebar layer. And you are right, there can of course be many more static additional considerations that you have to face, which slow down the construction project.
Dr. Oberhänsli: That’s another point that I have to make. The inversion of the question is to ask for which objects the CCP application makes no longer sense or what prevents a CCP from being used much more widely. The CCP is not an all-purpose weapon against objects that are not reaching their design life.
If we come to an object, where the static security can no longer be assured, because the residual rebar cross-section is already so limited that you have to add rebars or reinforce it, then it may be that the CCP really is not useful, because I anyway have to remove the concrete until the rebar to add
additional rebars, then it may be a more preventive protection for the future, but not in any case can a CCP be used as the solution. It is the case in many, many cases, but there are conditions that must be met.
Johannes: Do you have any other challenges when it comes to future applications of CCP systems? You have already mentioned the conviction of construction owners to understand the process. You also mentioned that the system is perhaps still not used enough, that it is not yet well known, although it has actually been around for a long time. Do you have any other challenges?
Dr. Oberhänsli: No, you have definitely anticipated them correctly. The one thing is the work of conviction with the appropriate experts. And the other thing is that the potential of cathodic corrosion protection, in my opinion, is not yet fully exploited or is being processed. There is still a lot to be done in this direction.
Johannes: I have to say that I am in your opinion. I think you are not only saying this because you are the CEO of Suicorr AG. I personally also have the feeling that the use of CCP is being presented as if it was a prestige project and something new. Where I also think that it should be the standard.
Johannes: One last question I forgot to ask before, which would interest me is: can you record the data? Because there is a potential between the steel reinforcement and the anode, from, as you said, either titanium or carbon, for example, can you record this data and could it be relevant? I think, for example, that different car parks have different weather influences or that different number of vehicles drive through rate. Can we compare, which construction method and exposure leads to accelerated corrosion? It would be interesting to use this data in the future.
Dr. Oberhänsli: I think that this can be a foundation for scientific work. At the CCP, I am obliged by international ISO standards to install a monitoring system and check regularly. This is actually intended to be done in a yearly tour.
And if we now break it down to the object, and not compare it in a scientific aspect to x-car parks, but for the object alone, it gives an incredible added value that I can make statements like, possibly, new moisture penetration points, how is my car park doing… I always exaggerate that we make a transparent object out of it and can look into the depths, whether corrosion has come to a halt or not.
These data enable me to give more actively change the CCP system, adjust the power supply and thus adjust the protection effect. And I think the CCP is very well positioned in this area, because these data are available and are being generated regularly. And there are various purposes. It is also partly state of the art that you then connect the cathodic corrosion protection system with BIM applications to prepare information of the whole object and generate and use it during the full life cycle. I think this will be enhanced in the future and we are already very well prepared for this.
Johannes: And this data is probably owned by the builder.
Dr. Oberhänsli: That is certainly the case and is to be regulated in the individual case, how to deal with this data.
Johannes: Daniel, thank you very much. It was very appealing. I didn’t announce too much at the beginning. I also learned something myself. I had a lot of fun. Thank you for being here.
Dr. Oberhänsli: I have to thank you. Thank you very much for the invitation. I was very happy, it was fun. And I look forward to all the comments, feedbacks, contacts, whatever. See you!
Johannes: See you, thank you!
Literature
- Korrosion von Autobahnbrücken in den USA kostet $ 8.3 Mrd pro Jahr –> Study initiated by NACE International and mandated by the U.S. Congress in late 1990s: “Corrosion Costs and Preventive Strategies in the Unitied States” PUBLICATION NO. FHWA-RD-01-156″
- Schweizer Brückenkorrosion kostet 1000 CHF/Minute: Korrosionsbedingte Kosten an Ingenieurbauwerken: ETHZ Research Collection
- Suicorr AG für Anfragen zu Kathodischen Korrosionschutz:
0 Comments